Every venturi style unit includes a machined injector or foamer body that is engineered for specific operating conditions. Discharge hoses (lengths and diameters), wands, nozzles and other components are carefully selected to ensure optimum system performance when paired with a balanced, or “matching”, injector or foamer body.
For proper performance do NOT modify or substitute the nozzle, hose diameter or hose length. Modifications can adversely affect the overall performance and/or dilution ratios. If your needs are not met by our standard product lineup, please contact us to discuss alternatives.
Below is a list of common modifications that often result in unsatisfactory performance. Note that using equipment “as provided” would prevent these issues.
Hose length too long
- Foamers and sprayers/sanitizers WILL work with longer hoses than supplied, but only if you have sufficient water pressure. Otherwise the extra solution in the longer hose puts too much back pressure on the venturi and it will not draw chemistry.
Hose length too short
- Compressed-air assisted foamers will NOT work properly with a shorter hose than supplied.
- The air and chemical solution mix to form rich foam as the solution travels through the full length of the discharge hose, so a shorter hose typically results in wetter (less rich) foam.
- Refer to the minimum hose length indicated on specific models.
- Sprayers/sanitizers and airless foamers WILL work with a shorter hose than supplied.
Hose diameter too small
- Foamers and sprayers/sanitizers will NOT work properly with a smaller diameter hose than supplied. A smaller diameter hose puts too much back pressure on the venturi and it will not draw chemistry.
Un-Balanced Discharge Assembly
- If you put a smaller nozzle on the wand “for extra distance”, foamers and sprayers/sanitizers will NOT work. A smaller nozzle puts too much back pressure on the venturi and it will not draw chemistry.
- Using an aftermarket trigger gun or alternate discharge assembly on the end of a foam hose will cause the foam quality to decrease.
Aside from modifications to the unit it is essential to ensure that the facility utilities, and even the chemicals, are suited for the task at hand. Here are some common sources of interference that can disrupt the system balance and cause undesired operation.
Undersized water supply lines
- The equipment will not perform as intended if the water supply lines are not large enough to allow an adequate volume of water to reach the unit.
- If your unit is designed to flow at less than 4 GPM then a 1/2″ water supply line is adequate.
- If the flow rate is higher than 4 GPM then a 3/4″ supply line will be needed.
- If over 10 GPM then a 1″ supply line is required.
Inadequate water pressure
- Ensure that your water supply can meet the minimum water pressure requirements for the selected unit.
- Most city water units show a minimum water pressure requirement of 35 PSI. This refers to the “dynamic” water pressure when the unit is operating. It is NOT the “static” pressure of the water line with the unit turned off.
- Ensure that the inlet ball valve is completely open. Do not open the valve partially to control output volume and/or pressure.
- Water pressure/flow test kits are available. Units can be fitted with in-line gauges to monitor water and air pressure.
Thick chemicals
- Metering tip charts are provided with water thin chemicals as a reference. Thicker chemicals will require a larger metering tip than indicated in the chart.
- Thick chemicals may require a larger diameter chemical check valve and chemical pick-up tube to allow the chemical to be drawn into the unit.
- Viscous chemical pickup tube kits include 1/2″ tubing.
Learn More about viscous chemicals with our VIDEO WALKTHROUGH.
Debris from water supply
- Obstructed injector orifices will result in equipment malfunction or poor/inconsistent performance.
- New piping (air and water) may contain debris from unit installation or building construction. It is important to flush out new piping before installing a unit or debris will likely enter and obstruct the liquid or air flow.
- Older piping is also likely to contain contaminants from various sources.
- Install an air and/or water filter to prevent debris from entering the unit.
Water too hot
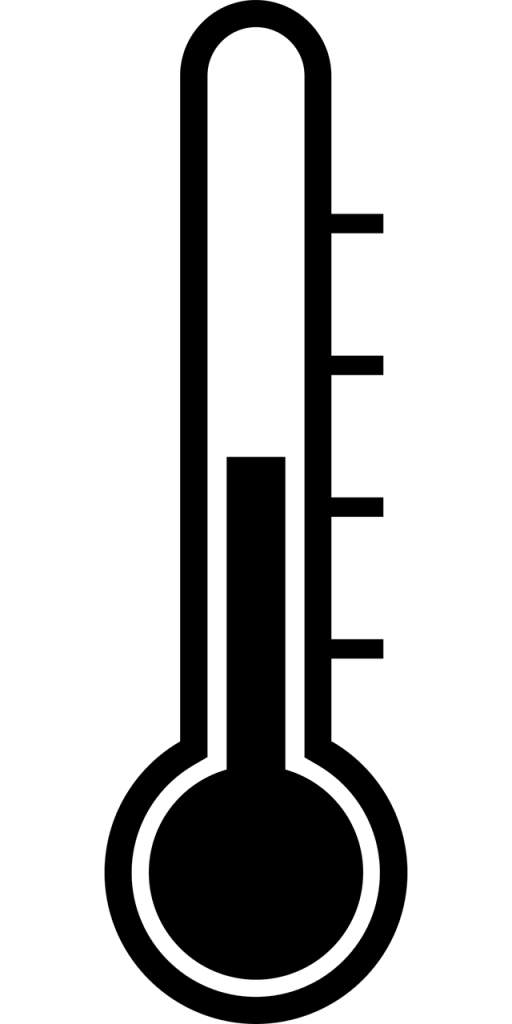
- When very hot water passes through a venturi body, the pressure reduction causes hot water to “flash” which is essentially water boiling and releasing water vapor into the system.
- This steam will prevent the venturi from properly drawing chemical and the output will sputter. An audible hissing or popping can be heard coming from the unit if this is occurring.
- Stainless steel injector and foamer bodies are able to handle higher water temperatures than polypropylene bodies, but water will still “flash” if the temperature is too high.
Pick-up tube damaged
- Suction will decrease if air is allowed to enter the chemical pick-up tube.
- This can be caused by the pick-up tube sliding down and not completely attaching to the unit intake or by a hole in the pick-up tube.
- Even a very small, pin sized hole will affect the suction.
NOTE: These are general troubleshooting tips. Please refer to the Installation and Operation Instructions for product specific installation guidelines, chemical dilution assistance, and troubleshooting.