Properties and Benefits of Foam
- Fundamentally, in the context of chemical cleaning, foam a mixture of water, chemical, and air.
- Foam clings to surfaces longer than liquid spray and increases chemical contact time.
- Foaming expands the chemical, allowing less chemical to cover more surface area.
- Foam prevents over-application by providing visual confirmation of coverage.
- Foam is projected at a lower pressure than liquid spray and can be used on more sensitive surfaces.

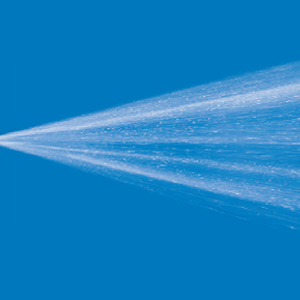
There are many reasons to apply chemicals as foam instead of as liquid spray. However, keep in mind that foaming may not be the ideal application method for your particular chemical type or application needs (spraying or fogging may be more appropriate).
Cleaning objectives, chemical properties, and the available utilities (compressed air) will determine which type of foam equipment is best for the job.
Types of Foam
Foam consistency (wet versus dry) plays a key role in maximizing the effectiveness of foam cleaning procedures. To appreciate the benefits, it is helpful to understand the different types of foam.
Airless Foam
Foam is created by drawing atmospheric air into the chemical solution via an Airless Foam Wand. Airless foam is a “wet” foam that allows the chemical solution to thoroughly penetrate soil/grime and facilitate removal.
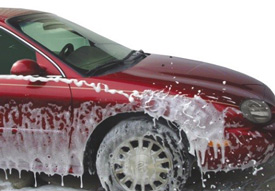
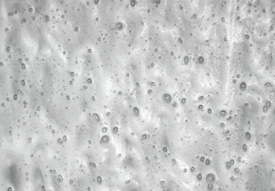
Depending on the chemical, Airless foam may not look as impressive as air-assisted foam. However, the chemical is still being applied more effectively than spraying liquid (which runs off the surface almost immediately, reducing wet contact time).
Airless Foamers do not require compressed air! The minimal installation and maintenance requirements are appropriate for almost any facility.
The foam quality of airless foamers is largely dependent upon the chemical dilution (strength) and foaming ability of the chemical. Overall performance can be refined by changing the chemical dilution and/or incoming water pressure.
Air-Assisted Foam
Rich, clinging foam is created by injecting compressed air into the chemical solution, which mix as they flow through the hose to the discharge wand and nozzle. Air-assisted foam is often described as “dry” because it can be highly aerated.
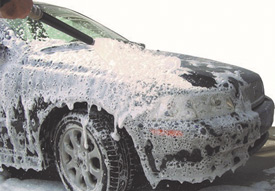
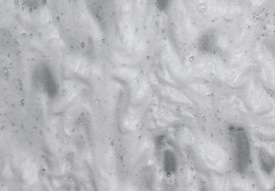
Air-assisted foam clings to surfaces longer than airless foam, but foam that is too dry will break up into clumps and not clean effectively. It is a best practice to use as little air as possible to generate the desired foam consistency.
A key advantage of air-assisted foamers is that the foam wetness can be adjusted on site, during operation, to suit a wide range of chemicals and coverage goals.
The foam quality and overall performance of air-assisted foamers can be adjusted by changing the chemical dilution, air pressure, and/or incoming water pressure.
Lafferty offers Airless and Air-Assisted Foamer configurations to dilute chemical on demand (Venturi) or utilize ready-to-use chemical (Pump Fed, Air Pump, etc.)
Foam Quality Troubleshooting
Not seeing the results you were hoping for? Consider these Frequently Asked Questions as well as the unit-specific troubleshooting guide in the Installation & Operation Instructions.
- Is the chemical designed for foaming?
- Foaming agents can be added to enhance the foaming properties of non-foaming or low-foaming chemicals.
- Is the chemical designed to foam well at the desired concentration (dilution ratio)?
- It may be necessary to increase the chemical concentration or add a foaming agent to enhance the overall foaming properties of the solution.
- Is the compressed air too high or too low?
- Adjust the air valve as needed to make the foam wetter or drier.
- Too much compressed air will produce a very dry foam that will not clean effectively. With too much air, the discharge hose may “buck” and foam output will sputter and behave inconsistently.
- Too little compressed air will produce a watery foam that will not cling to surfaces well.
- Adjust the air valve as needed to make the foam wetter or drier.
Troubleshooting Examples
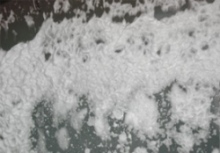
(Air-Assisted Only)
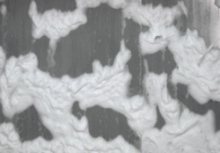
(Air-Assisted Only)
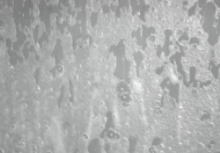